Laboratory Equipment
Equipment used by the CMML research group
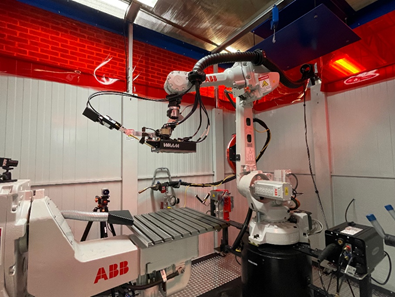
ABB FlexArc 250A (WAAM)
The ABB FlexArc 250A is a robotic welding cell utilized by CAVS for wire-arc additive manufacturing (WAAM). The cell consists of a 6-axis robotic arm and 2-axis positioner made by ABB, a Fronius TPS 400i cold metal transfer (CMT) power source, a Fronius TransTig 3000 and Plasma Module 10 Plasma arc welding (PAW) power source. Current thermal monitoring is performed using K-type thermocouples and an Optris PI400i infrared camera. An end effector built by WAAM3D is being acquired with the capability of providing trailing shielding gas as well as melt pool temperature monitoring for the PAW process.
CMML is currently utilizing the WAAM setup to build components using M250 maraging steel. Thermal history data is recorded from builds to verify finite element models of the process. Residual stress, microstructure composition, and mechanical properties are also determined from these builds using a variety of methods. Primary build geometry currently consists of thin walls and cylinders with plans to scale to large (200kg) and complex parts in the near future.
Renishaw AM400
The Renishaw AM400 is a selective laser melting (SLM) 3-D printer that utilizes the laser powder bed fusion (L-PBF) additive manufacturing (AM) process. In the L-PBF process, metal powder is spread in a thin layer across a substrate of the same material. Then, the powder is melted by scanning the dimensions of the part with a high-power laser. This process is repeated until the full volume of the metal part has been 3-D printed. The AM400 operates in a fully inert argon atmosphere and is capable of printing various materials such as Stainless Steel, Titanium, Aluminum, and Inconel.
CMML is using the Renishaw AM400 to conduct research on a variety of topics related to SLM AM. Some of these topics involve the SLM process, such as the effect of different processing parameters on the residual stress induced in SLM printed Ti6Al4V products and the impact of dwell time during the L-PBF process. Other topics involve parts produced using the SLM process, such as lattice structures and dog bones to be used in mechanical testing for model calibration.

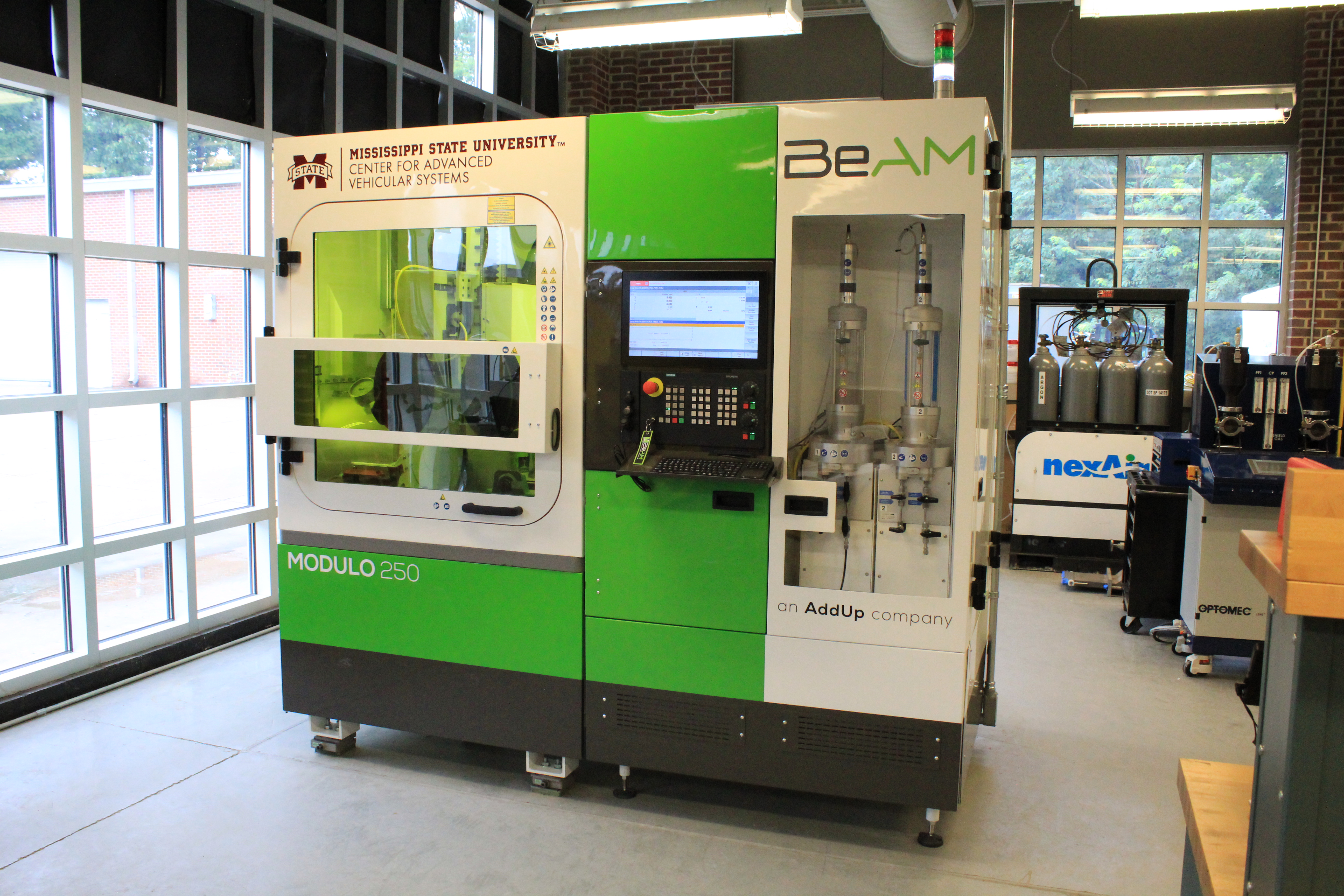
BeAM Modulo 250
The BeAM Modulo 250 uses an AM technology known as Directed Energy Deposition (DED) that focuses thermal energy in the form of a laser to melt metal powder as it is being deposited. Specially designed for the activities of R&D, training, and the production of small dimension parts, the BeAM Modulo 250 offers the ability to create Functionally Graded Materials (FGM) by printing multiple powders at once. Although other AM systems can produce FGMs, the BeAM can do this much more easily and readily due to the dual powder feeder. Metal parts produced on the BeAM machine have a near net shape finish with no need for supports, allowing for less post processing and material waste.
CMML research with the BeAM includes microstructural characterization, improvements in process control parameters, and predicting residual stress and distortion in printed parts using FE software. The metal powders used in the BeAM include Ti-6Al-4V, IN625, IN718, and 316L. Future work will study the effects of bare laser tracing on substrates to obtain desired surface morphology.
Instron 5882
The Instron 5882 is an electromechanical testing system with a load frame capable of testing hardened steel. Tests that can be conducted include tension, compression, and flexure tests at various load rates and temperatures. This machine is leveraged by CMML for the mechanical characterization of additively manufactured parts to inform material modeling efforts and for the validation of computational results. The Instron 5882 is located within the solid mechanics lab at the Center for Advanced Vehicular Systems.
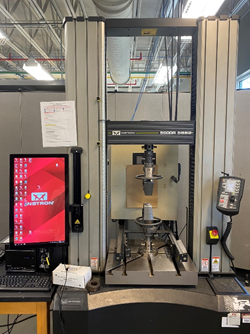
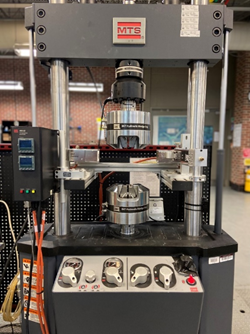
MTS Landmark
The MTS Landmark is a floor-mounted, hydraulic mechanical testing load frame. The system is capable of testing components at room and elevated temperatures.
The MTS Landmark is currently being used for high-temperature tensile testing of various metals including 316L stainless steel, Grade 2 Titanium, and M250 maraging steel. Testing is being performed in accordance with ASTM E21 using ASTM E8 flat subsize tensile specimens at various strain rates and temperatures. Data from this testing will ultimately be used to provide temperature dependent mechanical properties for thermomechanical simulations of additive manufacturing processes.
Wilson VH3100 Microhardness Indenter
The Wilson VH3100 microhardness testing system consists of an automated X/Y stage for determining hardness across a wide surface area. Hardness can be measured on either Knoop or Vickers scales, and the system can be automated to perform 150 indentations with calculated hardness values within an hour. The system has a 10x and a 50x objective that allows for clear resolution of the sample surface and measurement of indentations.
CMML uses the VH3100 for material characterization by calculating the hardness of specimens built using the L-PBF, WAAM, and DED additive manufacturing process.
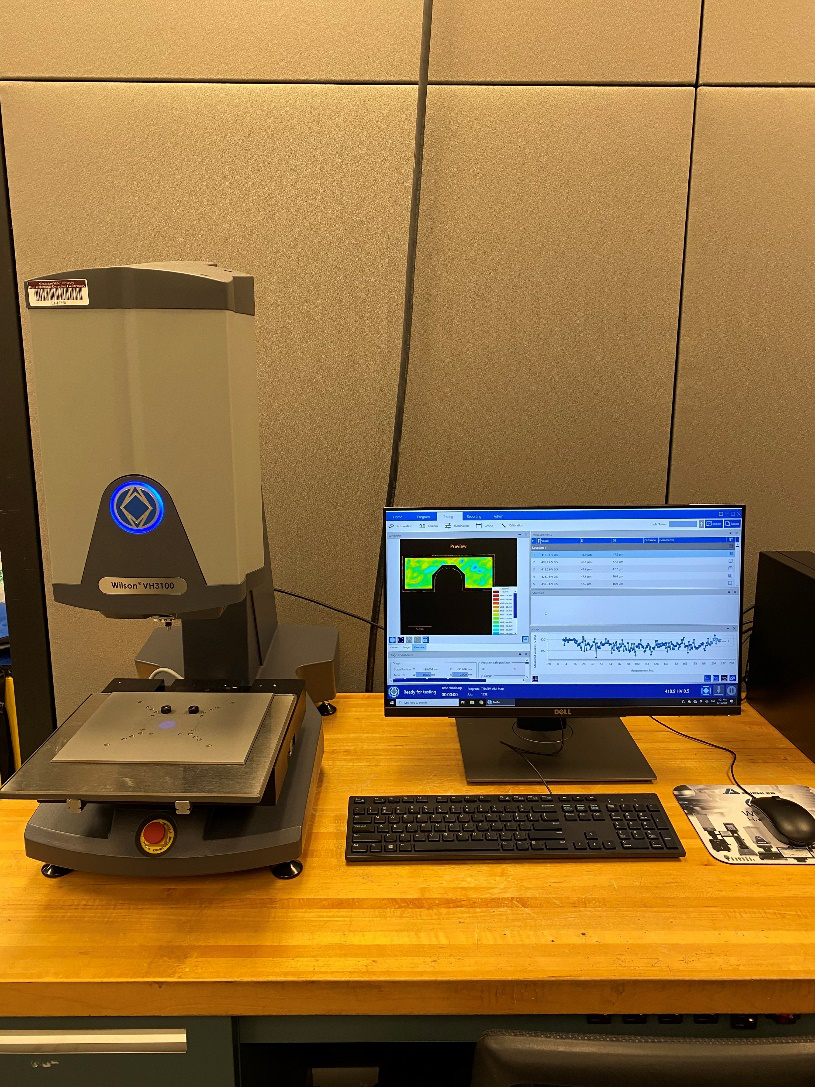
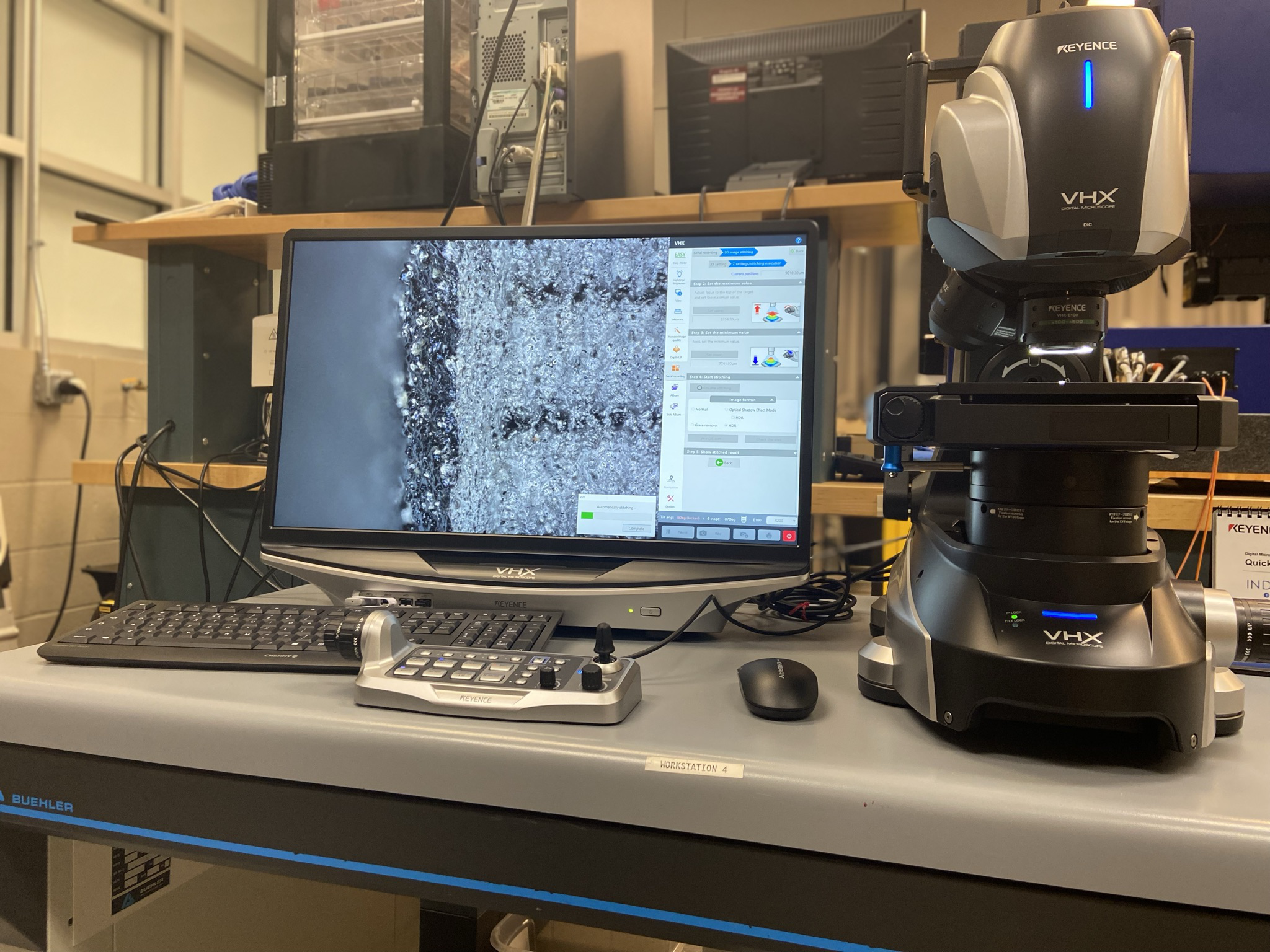
Keyence VHX-7000 (Digital Microscope)
The Keyence VHX-7000 is a 4K ultra-high accuracy microscope capable of 20x-5000x zoom. Unlike other digital microscopes, the VHX-7000 makes use of omnidirectional lighting to pick up subtle irregulates on a sample. Combining this with a depth of field 20x greater than conventional digital microscopes allow the VHX to images that rival SEM. The system can be used to generate 2D and 3D measurements as well as looking at crystal grain size measurement and automatic area measurement/count.
The Keyence Digital Microscope is a new arrival to our lab, but CMML has plans to utilize this equipment for microstructure analysis (average grain size, phase volume fraction, porosity/inclusion analysis) of additively manufactured steels and aluminums. Failure analysis of composite panels and tensile test specimens may be performed as well.
Keyence VR-5000 (Wide-Area 3D Measurement System)
The Keyence VR-5000 is a non-contact 3D optical profilometer that can measure wide areas quickly and accurately. Measurements can go up to 50 mm in height, over 5 times that of conventional systems. Multiple objects can be scanned simultaneously, or a single object up to 200 (L) x 100 (W) mm. The VR can automatically accommodate for object rotation and tilt, meaning nearly any complex geometry can be scanned. This includes screws, lattice structures and convex/concave components.
CMML has used the Keyence VR-5000 to analyze ballistic impact, measure the profile of bone screws, and look at surface roughness for magnesium degradation. We are actively using the VR-5000 to analyze residual stress in additively manufactured parts, using the contour method. The VR-5000 has also been used to perform general 3D measurements of tensile test specimens, as well as look at surface roughness on additively manufactured parts.
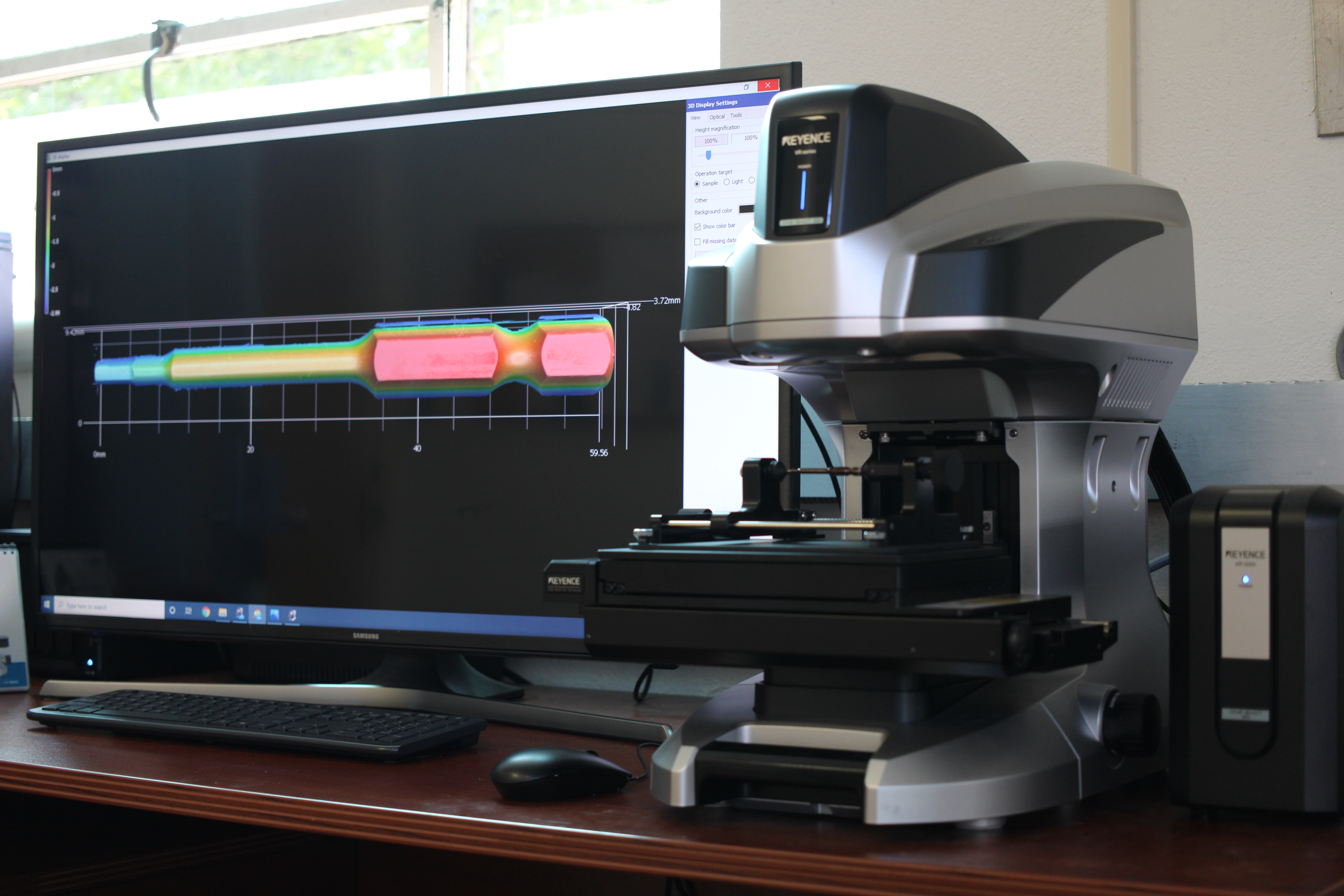
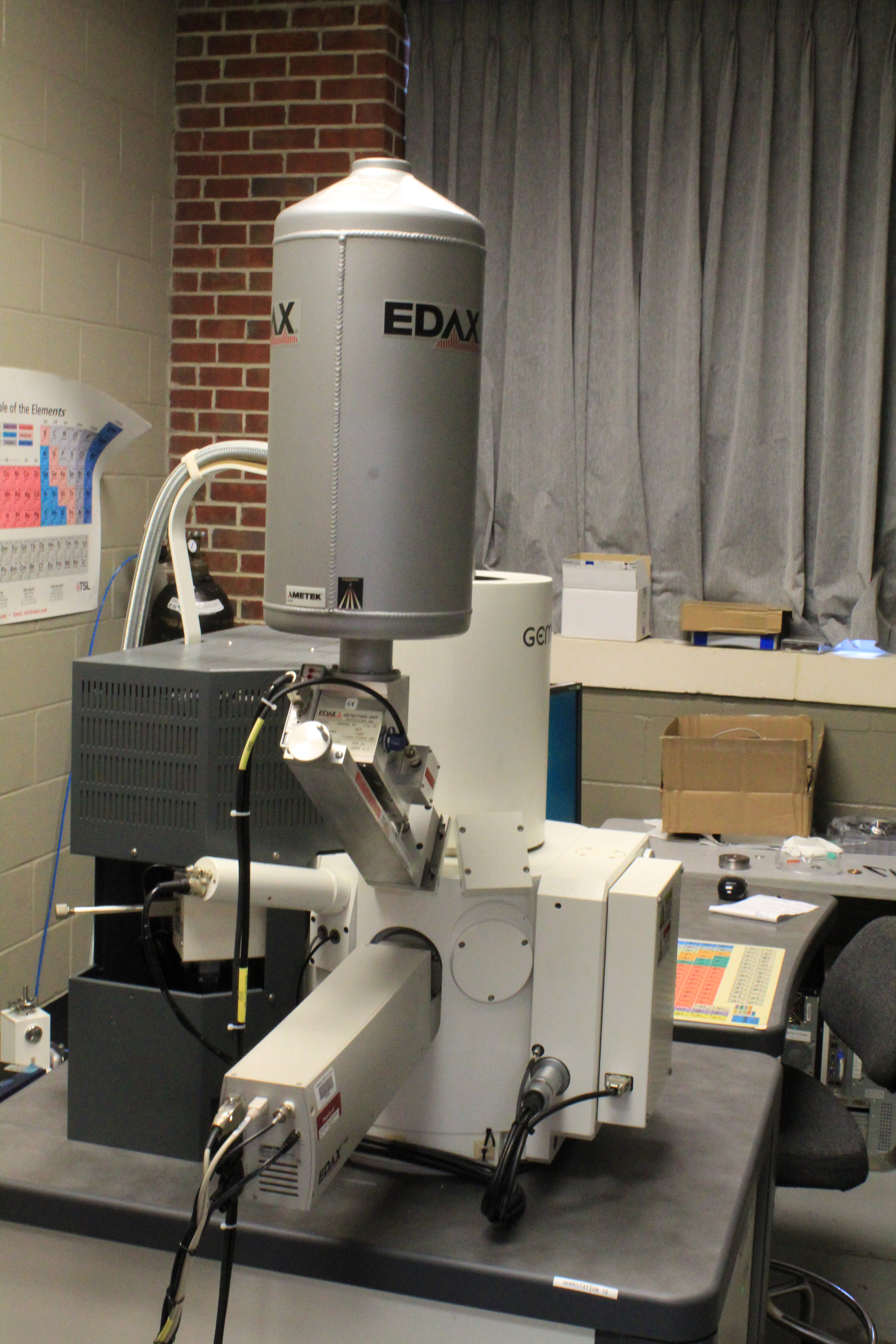
Zeiss Supra 40 Scanning Electron Microscope
The Supra 40 housed within MSU's CAVS/I2AT facility is a general purpose high resolution Field Emission Scanning Electron Microscope (FESEM). It is equipped with Energy Dispersive X-ray Spectroscopy (EDS) capabilities for elemental determination and an Electron Backscatter Diffraction (EBSD) camera for crystalline structure and crystallographic grain orientation examination.
CMML uses the Supra 40 to analyze the grain structure of additively manufactured metals and alloys, which exhibit varied microstructures when compared to traditionally made materials, which are crucial to understanding material properties.
Nikon XT H255 X-Ray Computed Tomography (XCT)
The Nikon XT H 225 housed within MSU's CAVS/I2AT facility can non-destructively provide information about the internal structure of materials on the micron scale. It uses the penetrating power of X-rays to obtain a series of 2D image projections of a sample specimen viewed from many different directions, which can then be reconstructed with an algorithm to create a digital 3D visualization of the specimen and its interior. This reconstruction can be quantitatively analyzed and virtually sliced in any direction to examine properties, such as morphology and volume density. This benefits a wide range of applications, including inspection of small castings, welds, plastic parts, porosity determination, and more.
CMML uses XCT to analyze the morphology, volume density, and porosity of additively manufactured materials and other specimens of interest to the group.
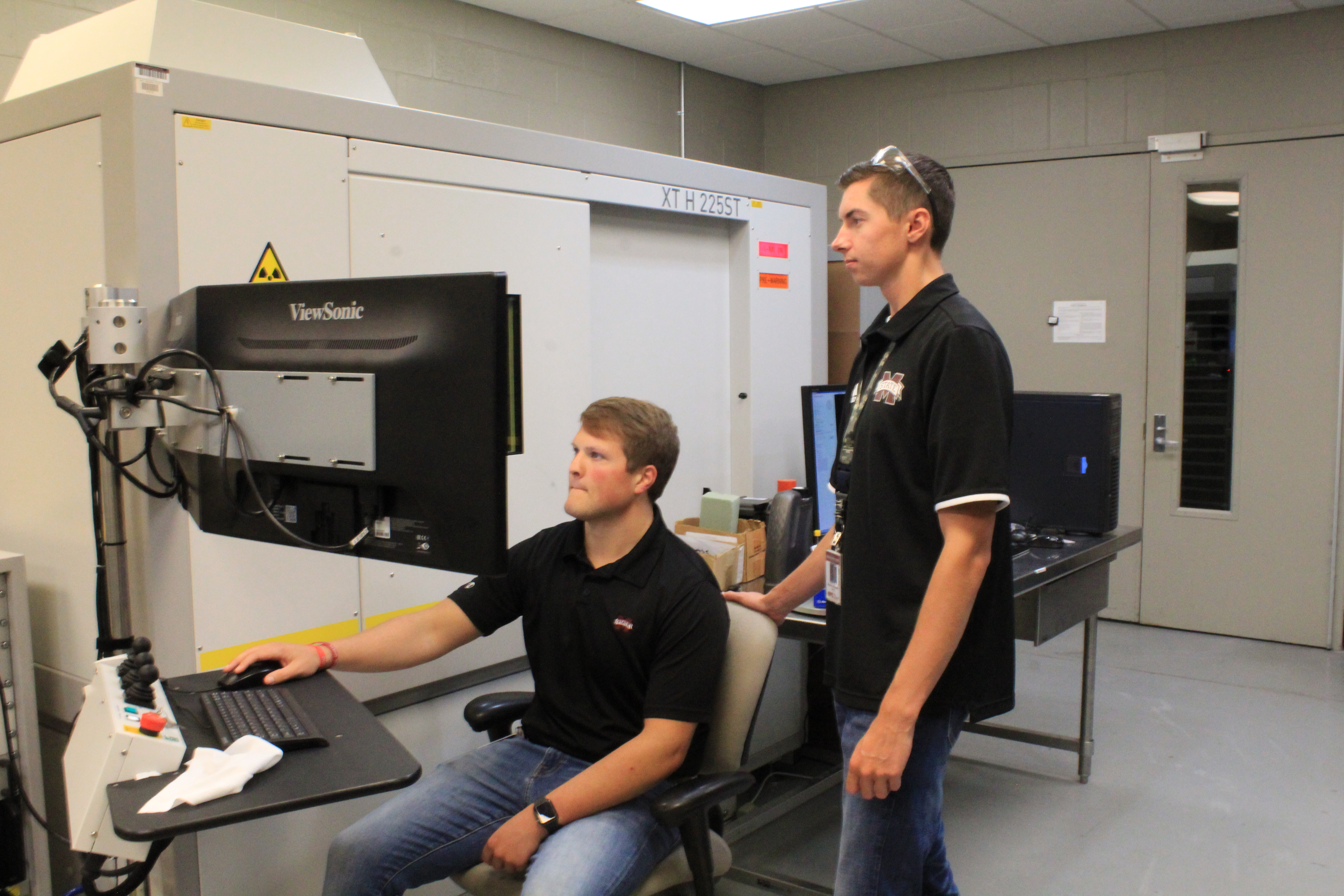
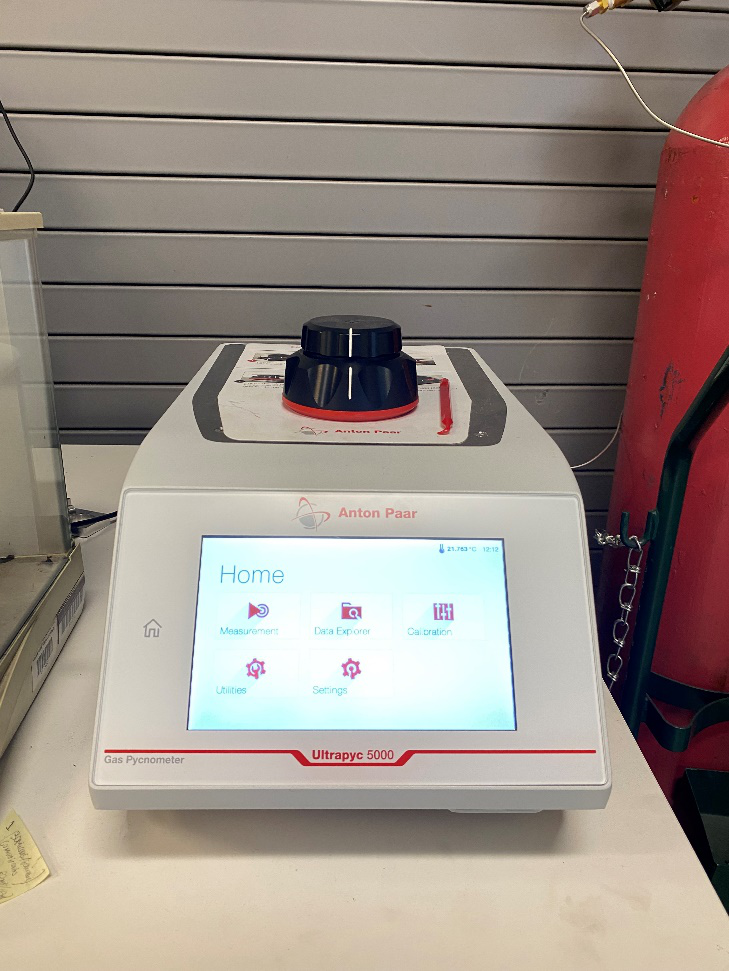
Anton Paar Ultrapyc 5000 Gas Pycnometer
The Anton Paar Ultrapyc 5000 gas pycnometer is housed within MSU's CAVS/I2AT facility and can measure the true and skeletal density of solids. The system fills a small chamber with helium and determines the volume that is occupied by the specimen. It then uses the mass of the specimen to calculate the specimen’s density. The system is useful for tracking the purity and porosity of solid materials.
CMML uses the Ultrapyc 5000 to determine the density of additively manufactured parts including lattice structures and tensile specimens, to better understand the purity and porosity of each part.