Relevant research focuses revolve around the computational modeling of material systems for energy absorption and material characterization methods. To advance this research and establish a relationship with AM, internal state variable (ISV) models such as the evolving microstructural model of inelasticity are introduced. For example, J-C models are not necessarily robust enough to account for the anisotropy and thermal softening involved with mechanical properties of many AM produced metals.
The primary task is then to derive a PSPP relationship map for a single material between L-PBF AM and protective systems. From there, a physically based constitutive model can be calibrated for the simulating of fabrication and dynamic loading of a protective system procured through L-PBF AM. For L-PBF AM, it is hypothesized that characterizing the cooling and solidifying rate effects on the grain size, shape, and distribution during the build process is the crux to developing the PSPP map for the primary task. With the calibrated model, extending the material development and modeling energy absorbent material systems should be intuitive. Once the initial goal for L-PBF AM and protective systems is achieved, the methodology can then be extended to solid-state and wire arc AM for the modeling and fabrication of larger parts.
Research Projects
Learn about some of the current and past research projects performed by the CMML research group
Computational Modeling of Additive Manufacturing Parts and Processes
Quantifying the relationship between process parameters and the resultant mechanical properties of additively manufactured material systems
Primary Student Researcher:
David Failla
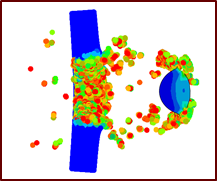
Hover image to expand
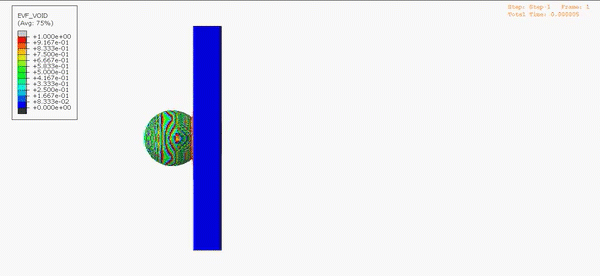
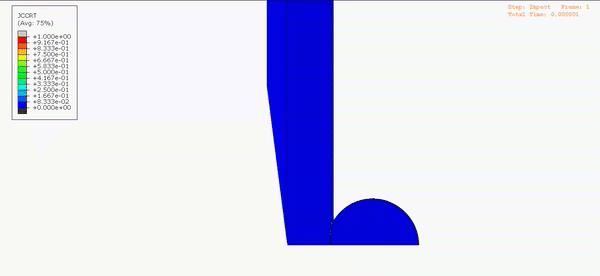
Fire Forensic Analysis of Aerospace Composites
Developing a novel surface treatment protocol for aircraft composites to analyze failure and post-crash fire damage
Primary Student Researcher:
Abhijith Madabhushi
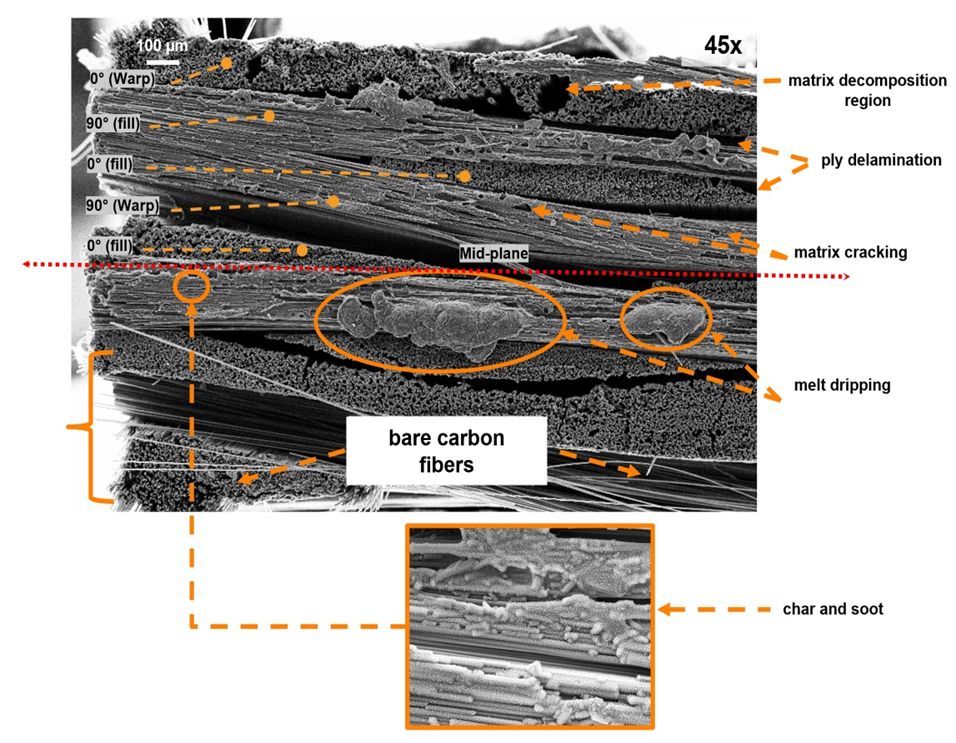
Hover image to expand
Composite aircraft structures are often subjected to both post-crash fire and complex multi-mode mechanical failures during a crash-event. During large-scale fires, the composite part's thermal damage is often catastrophic, and can mask the underlying fracture features due to severe fiber and matrix degradation and char formation. Therefore, there arises a need to develop an effective fire-damage assessment methodology to perform fire forensics on the burned aircraft structural elements, and assess the effect of fire damage on the fracture surfaces developed during mechanical failure.
The current project aims to analyze composite specimens subjected to various mechanical failure modes to identify the macroscopic and microscopic failure characteristics of the fracture surfaces. Then, a burning test protocol is developed for small-scale carbon/graphite reinforced epoxy specimens and identify the salient fire damage characteristics (i.e., melt dripping, char, and soot deposition, etc.). Finally, a surface treatment protocol is refined for the removal of the fire damage remnants (char and soot, melt dripping).
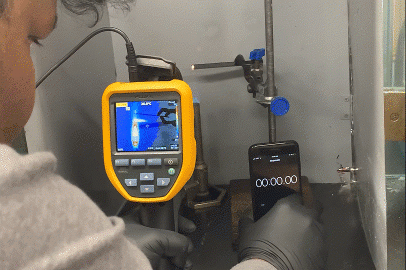
Coupled Thermo-Mechanical Approach to Model and Predict Distortions of Wire Arc Additively Manufacturing Parts
Producing a finite element thermomechanical model that can accurately predict residual stresses and distortion in as-built parts manufactured via the wire arc additive manufacturing process
Primary Student Researcher:
Matthew Register
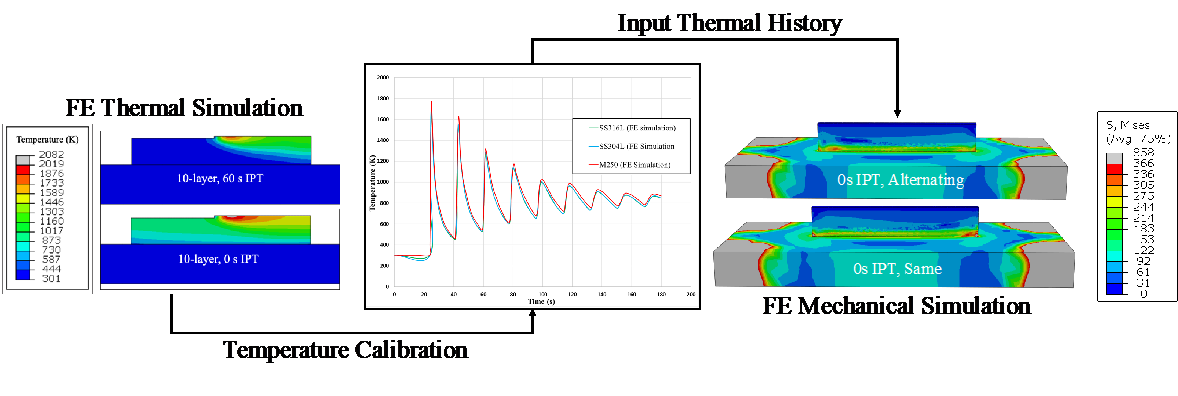
Hover image to expand
Wire arc additive manufacturing (WAAM) is a process that involves the melting of wire using an arc as the heat source. WAAM has the ability to make large scale parts with a high deposition rate. This process saves both time and material cost; however, one main issue is the high heat concentration related to WAAM which can result in poor part quality. Residual stresses and distortions can be found in many built parts due to the high heat concentrations.
To predict the stresses and distortions in the part, a finite element (FE) thermo-mechanical model is used to simulate the WAAM process. First, an FE thermal model is created to simulate the arc melting the wire along the print path. The temperature data gathered from the simulation is calibrated by comparison to experimental temperature data. Using the calibrated temperature history and mechanical material properties, an FE mechanical model is made which can predict the stresses on the built part. The stress data is then compared between the simulation and experimental results in order to determine accuracy.
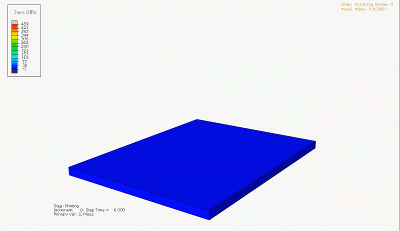
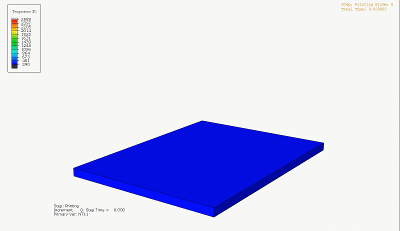
Geomaterial Characterization through Multi-spectral Electromagnetic Modeling
Characterizing geomaterials' electromagnetic signatures and predicting composition through computational electromagnetic modeling
Primary Student Researcher:
Patrick Camacho
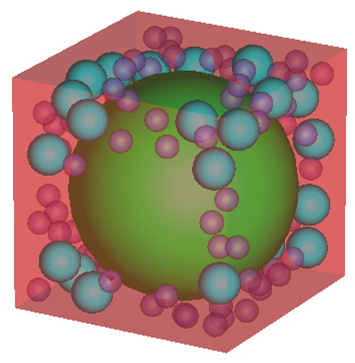
Hover image to expand
There is a need for a far-reaching, non-destructive test method to determine properties of structures. Present non-nondestructive methods apply mechanical or electromagnetic principles for inspections but are limited by the need of being in close proximity to the structure. Furthermore, the present electromagnetic techniques primarily function as fault identification or condition-based monitoring.
This work aims to develop a tool to link a material's electromagnetic signature to its physical properties. The approach this effort is taking is developing a statistical model based on the multi-spectral electromagnetic responses from high frequency simulations of micro/meso-structure element models for geomaterials. A fully developed model is expected to approximately predict physical properties such as an elastic modulus and or volume fractions of constituents by linking the electromagnetic signatures to the characteristics of the microstructure of the geomaterial.
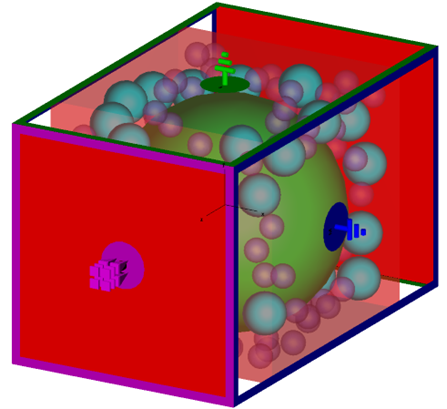
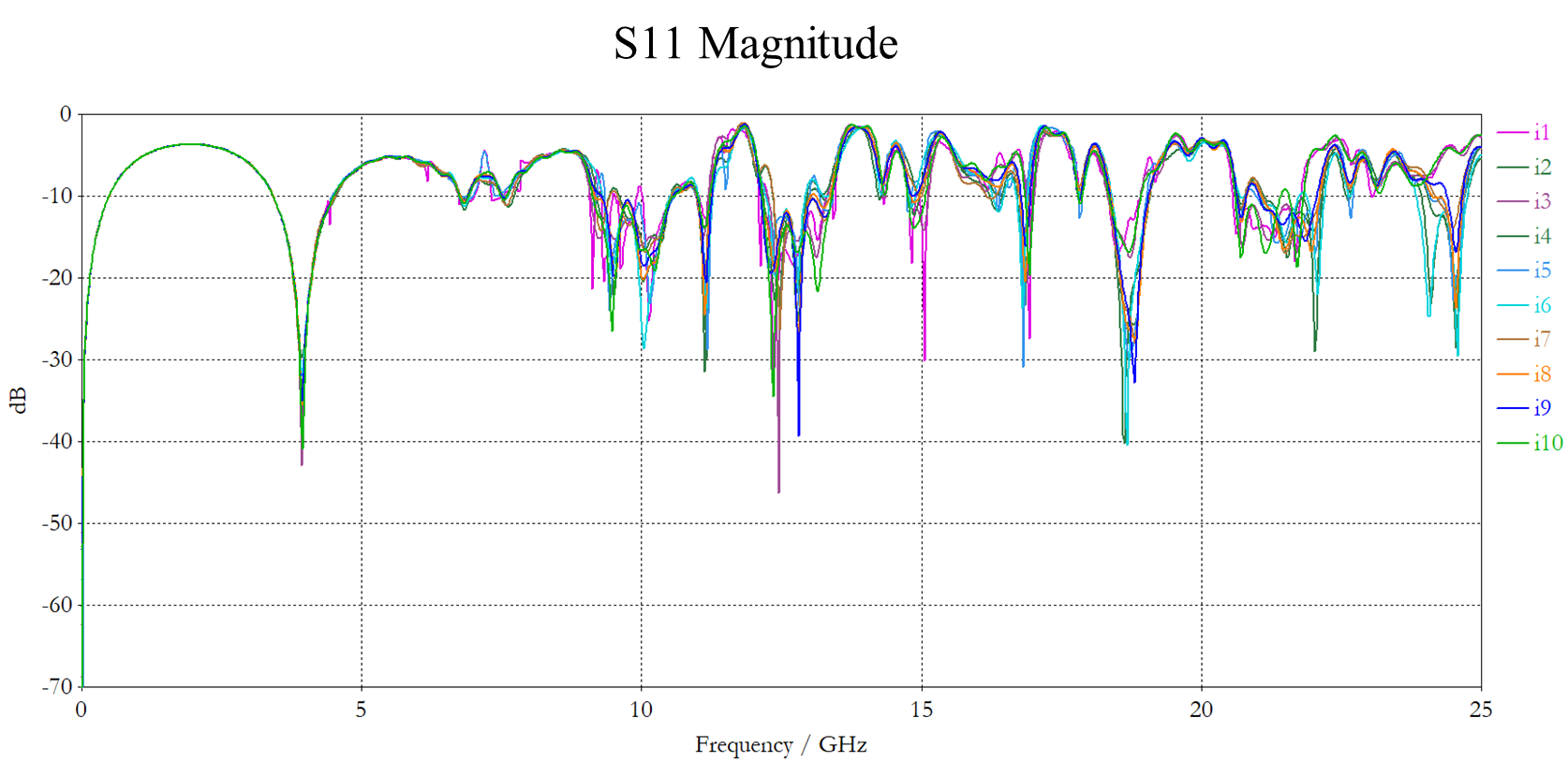
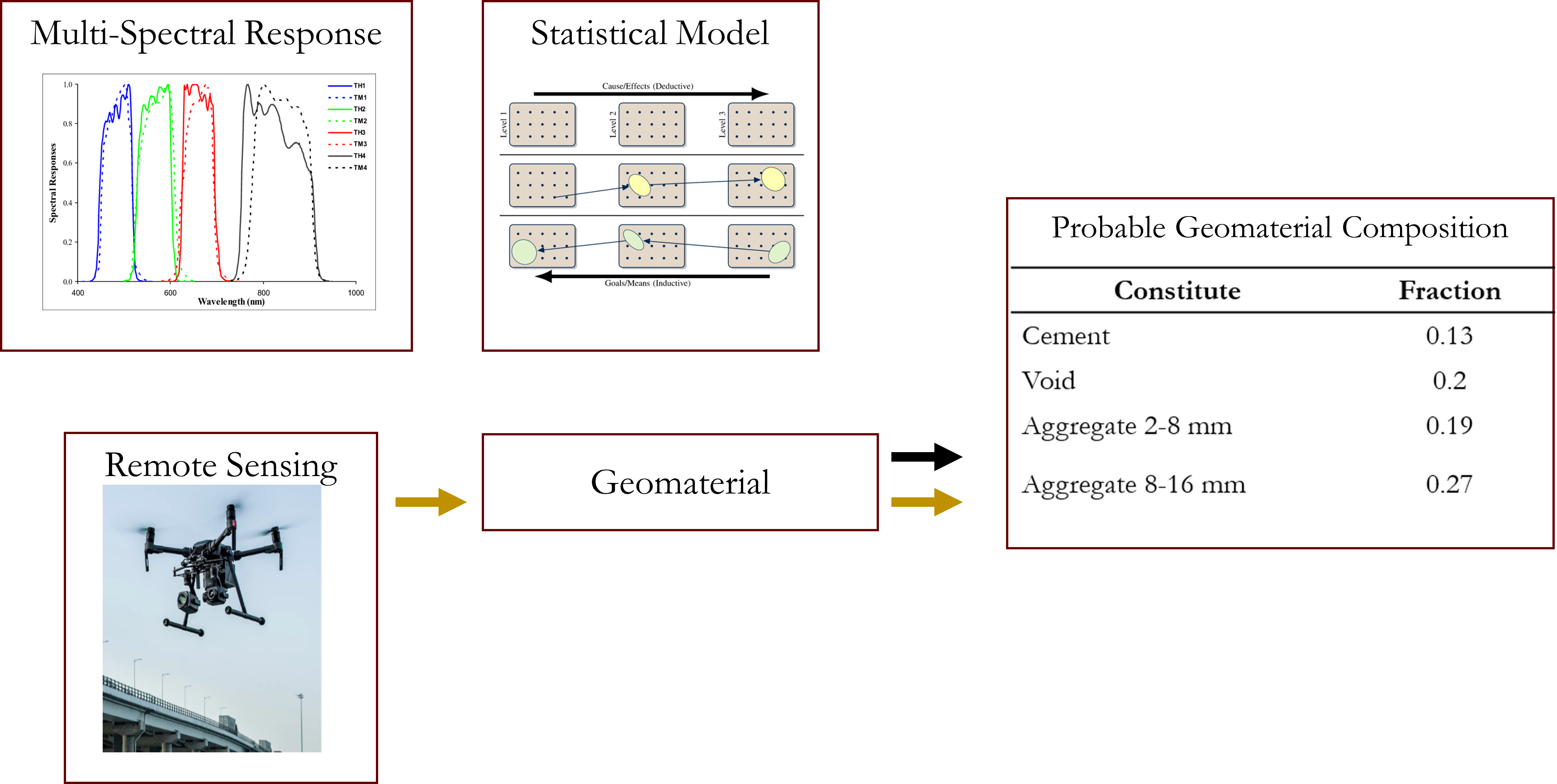
Finite Element Thermomechanical Modeling of the Directed Energy Deposition Process
Predicting the mechanical response of an as-built Ti-6Al-4V directed energy deposition component by a dislocation mechanics-based internal state variable model based on the component's geometry and processing parameters
Primary Student Researcher:
Matthew Dantin
Link to Published Research
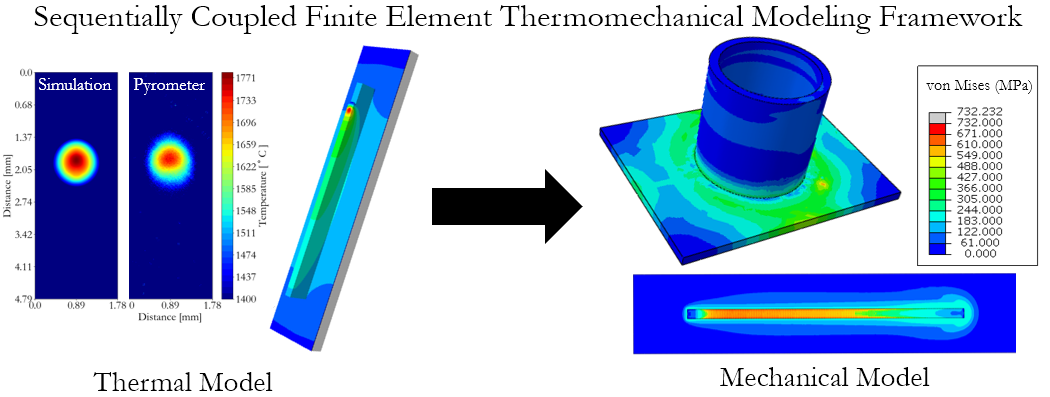
Hover image to expand
Research has been performed to connect additive manufacturing (AM) process parameters including laser power and scanning strategy to different aspects of part quality, such as porosity, mechanical properties, fatigue life, microstructure, residual stresses, and distortion. The lack of predictive capabilities to fully estimate residual stresses and distortion within parts produced via AM have hindered part qualification; however, modeling the AM process can aide in process and geometry optimization compared to traditional trial-and-error methods. The presence of unwanted thermally induced residual stresses and distortion can lead to tolerancing issues, reduced fatigue life, and decreased mechanical performance compared to similar components fabricated with traditional manufacturing methods such as casting and machining.
Directed energy deposition (DED) is a type of metal-based AM, characterized by a blown powder feedstock and a laser heat source. A sequentially-coupled thermomechanical model simulating the DED process has been constructed in Abaqus and has been calibrated using dual-wave pyrometer thermal image datasets along with temperature- and strain rate-dependent mechanical data. The purpose of this work is to understand the relationship between a component's temperature history and its resultant distortion and residual stresses.
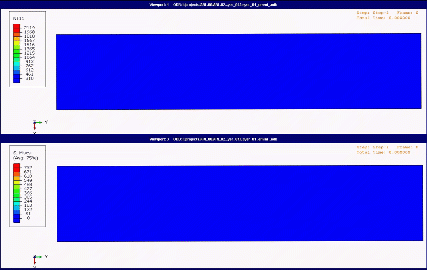
Mechanical Characterization of Functionally Graded Cellular Structures
Using a combined experimental and numerical approach to characterize the mechanical response and deformation mechanism of cellular structures designed with a graded relative density
Primary Student Researcher:
Brad Sampson
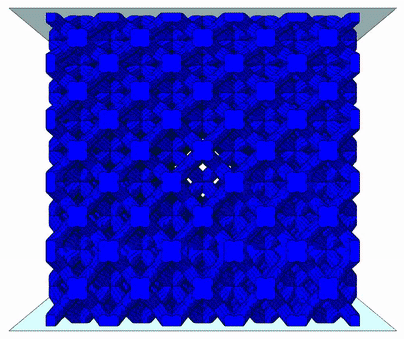
Hover image to expand
With a layered process like laser powder bed fusion (L-PBF) additive manufacturing, geometries with complex internal features such as cellular structures can be manufactured with a high geometric accuracy. Cellular structures, or lattice structures, are made up of a repeating array of unit cells based on a specified unit cell geometry, dimensions, and volume fraction. These highly customizable structures possess a high strength to weight ratio, energy absorption capacity, and superior heat dissipation are being utilized in the aerospace, biomedical, and defense industries.
Current research being conducted within CMML includes improving the specific energy absorption of materials through functional graded cellular structures. Characterization techniques include compression testing to measure mechanical response, digital image correlation (DIC) to identify deformation mechanism, microscopy to evaluate geometric accuracy, and finite element analysis to predict the mechanical response additional lattice geometry variants.
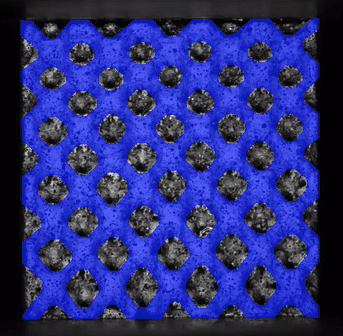
Sponsors
We would like to thank the following sponsors for providing funding for the research performed in this group:
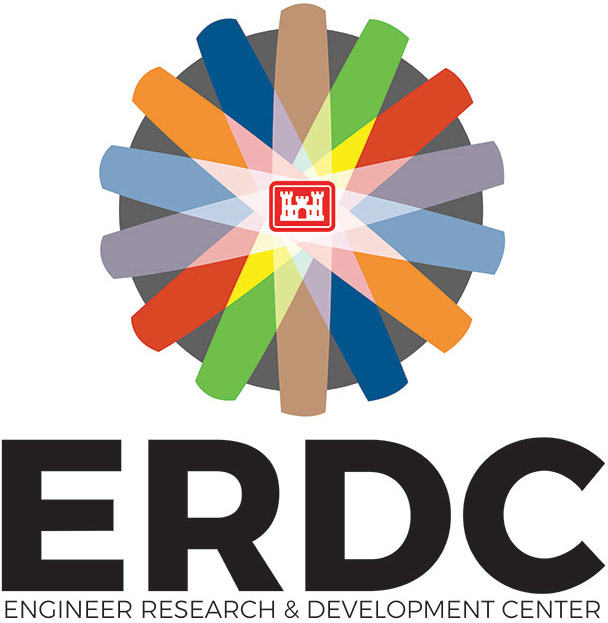
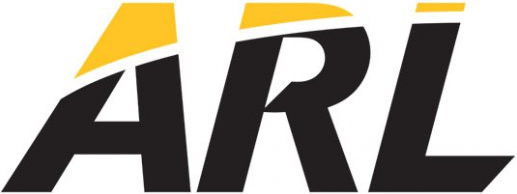
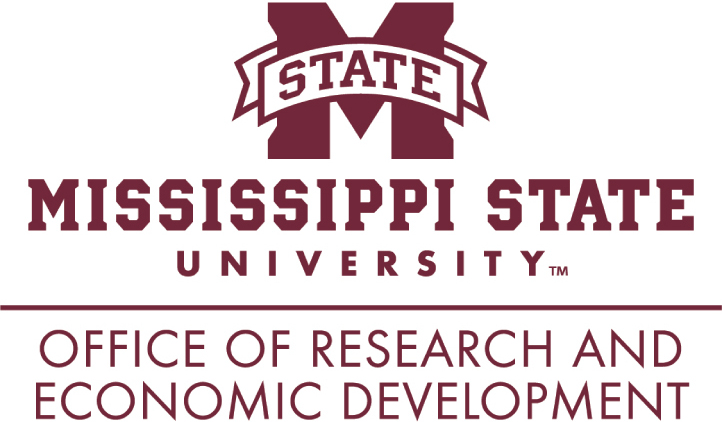
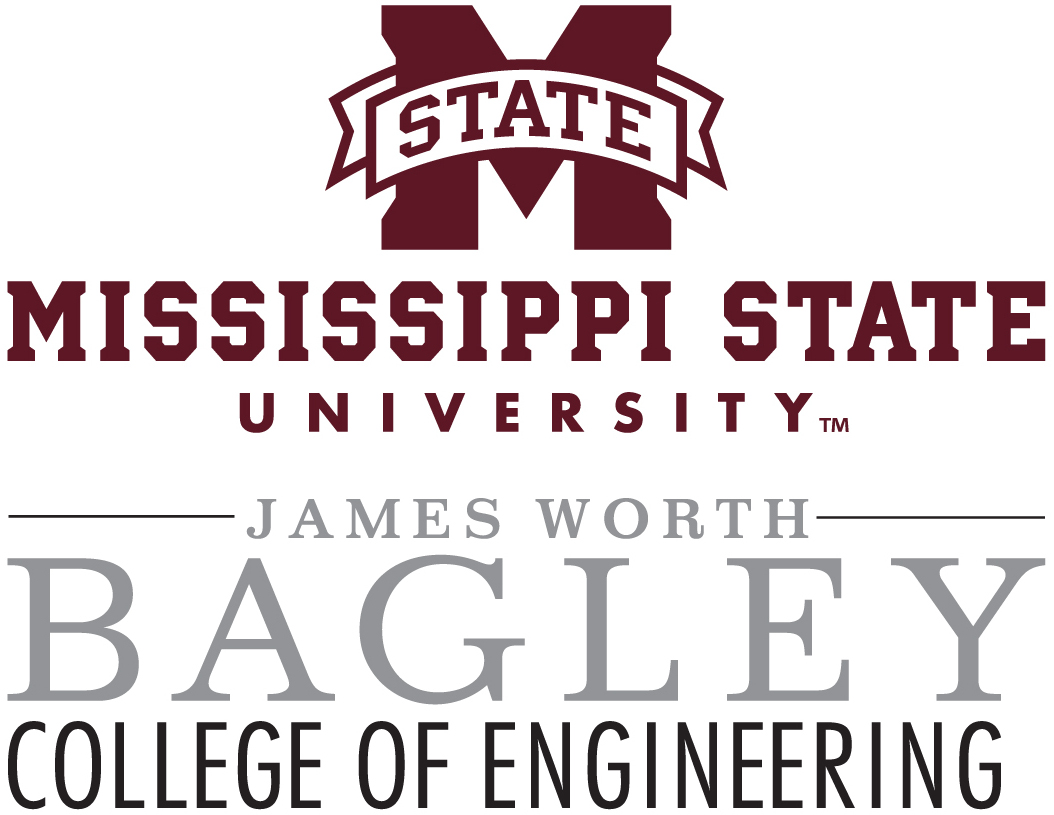
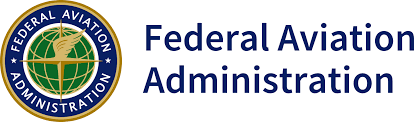
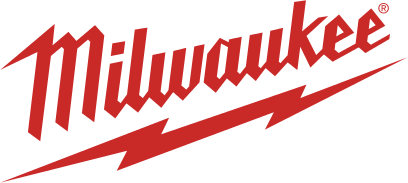

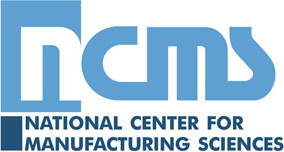